Trakonta ltd, 54031 Ukraine, Nikolaiv city, Electronnay street 81/4, E-mail: trakonta@gmail.com Tel: +380512714945; Mob, Viber: +380503180260
Electrohydropulse technology for crushing materials
Electro-hydraulic crushing is a new method of crushing various materials, it allows to obtain a given crushing degree at a certain granulometric composition of the product and has a high crushing selectivity.
Trakonta ltd
Electrohydropulse technology for crushing materials
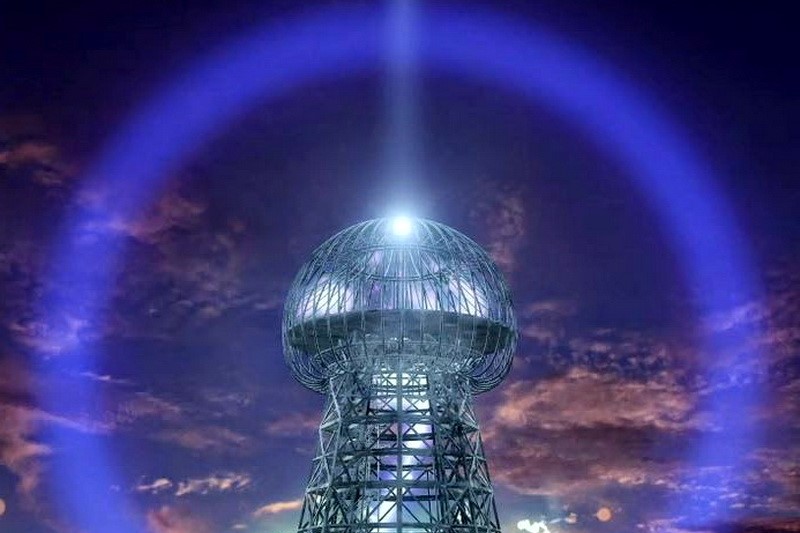
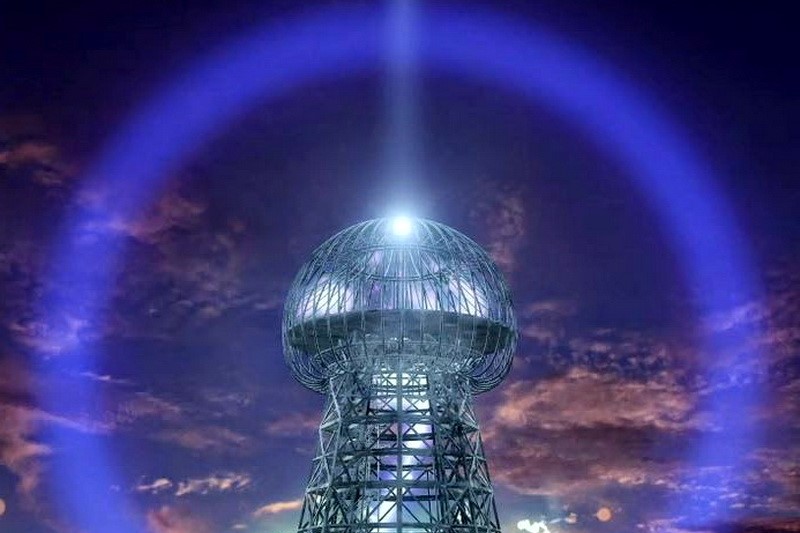
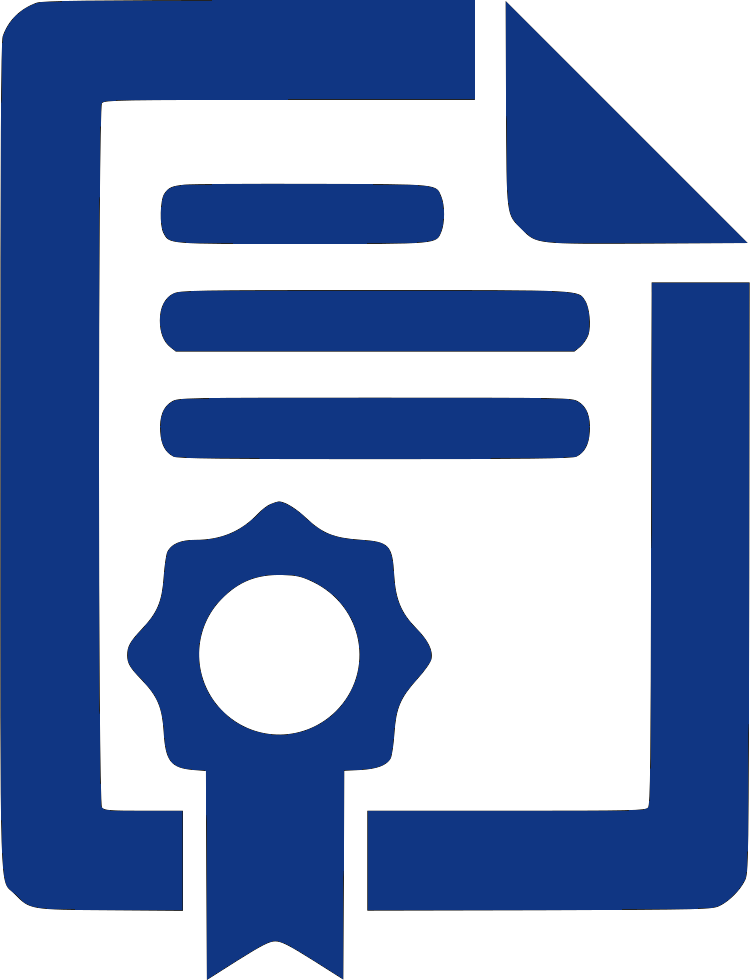
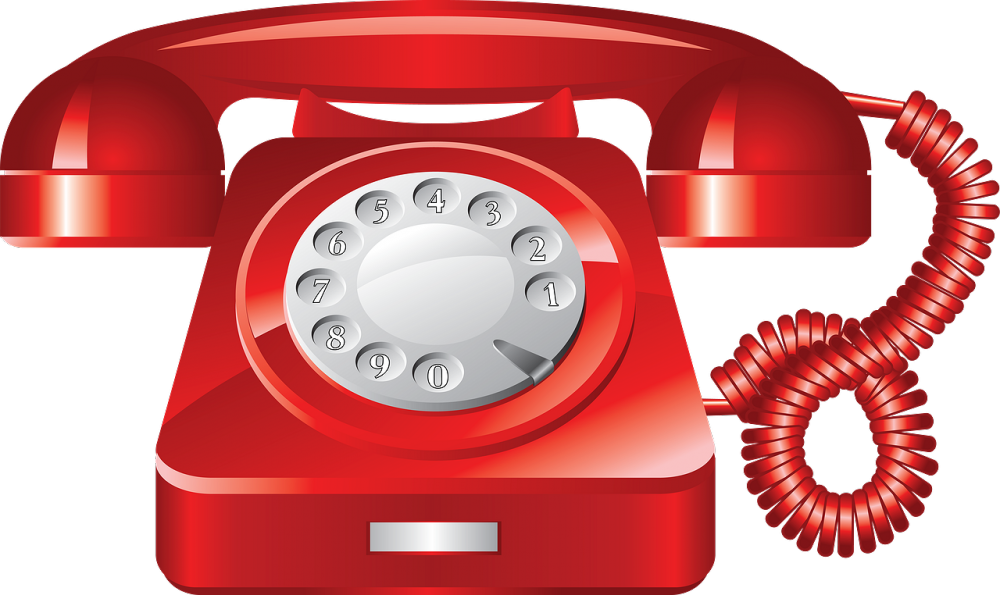

![]()
Electro-hydraulic crushing devices, unlike mechanical crushers, have no moving parts, are made of ordinary structural steel, and their body practically does not wear out during operation. During operation, these devices do not generate dust, occupy a relatively small production area and allow the combination of crushing, mixing and flotation of materials in them. Any liquid (mainly industrial water) can serve as a working medium in electro-hydraulic crushers.
The technological process of electro-hydraulic crushing is easy to automate, and a large number of highly skilled workers are not required to service the electro-hydraulic crusher. In electro-hydraulic crushers, you can crush and grind almost any material: rocks, coal, asbestos, mica, paper, cement, grain, peat, roughage, brittle metals, destroy microorganisms, extract diamonds from kimberlites, cultivate the soil and perform other work. Crushers are becoming more and more widespread in all areas of the national economy.
In this regard, the electro-hydraulic crushing method into coarse fractions is less profitable compared to existing crushing methods and, conversely, with an increase in the degree of crushing, electro-hydraulic crushing becomes the most profitable method.
The different types of electrohydraulic crushers are classified primarily according to the type of material being electrohydraulically processed. Each type of material has its own crushing method:
1) crushers for solid non-conductive materials (stone, cement, porcelain); crushing is carried out by the "internal blow" method;
2) crushers for hard brittle conductive materials (hard alloys, carbides); crushing is carried out by the methods of "joint crushing" and "external impact";
3) crushers for elastic, fibrous and elastic materials (paper, rubber, wood, peat and other organic materials); crushing is most expedient to produce by the methods of "air cavitation" and "bubble cumulation".
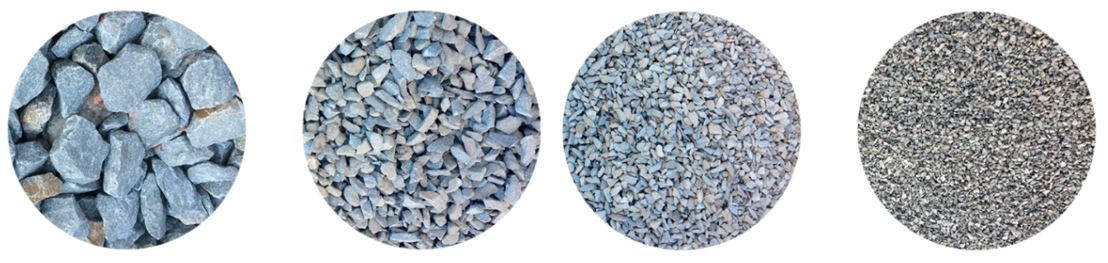
From the peculiarities of the processes of electrohydraulic crushing, it follows that the efficiency of the crusher itself will be as higher, as smaller the fractions of the material it is intended to produce and as smaller the sizes of the fractions of the initial material. This is explained by the fact that the spark gives off energy by its surface, and therefore, the denser the material surrounds the discharge zone (the more finely crushed it is), the more efficiently and fully the energy released by the discharge channel is spent.
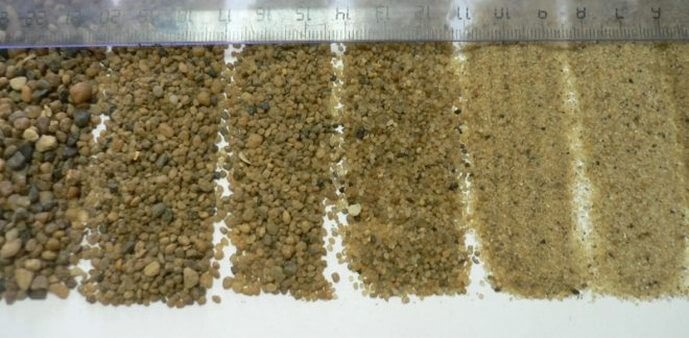
Methods and devices have also been developed for crushing metallurgical slags and kimberlites, colloidal grinding of metals and their compounds, colloidal dressing of ores and mining materials. All types of crushers also differ in the degree of crushing of materials to fractions of a certain size (crushed stone, sand, colloidal) and structurally - depending on the location of the positive electrode, which can be top, side or bottom. The negative electrode is almost always the crusher body. Material loading can also be top, bottom and side.
All electro-hydraulic crushers can work as mixers, and some of them, in addition to crushing, can also carry out the flotation process. Crushing units can be structurally performed and combined. In this case, they are enclosed in one common housing with several electrodes and a common loading device.
When crushing rocks, selective destruction is essential. This is due to the fact that traditional mechanical methods of destruction do not have selectivity when using them.
There is a partial violation of the forms of crystals and grains of the extracted minerals, as well as contamination of the processed products with apparatus metal. Selective destruction of rocks containing precious raw materials (diamonds, gold, etc.) allows the separation of useful components from the host rock while preserving the natural forms of minerals. In many cases, the chemical purity of the processed products (quartz, ceramics, etc.) is required.
Traditional crushing and grinding equipment does not have selectivity of destruction and is mainly intended to reduce the size of the feedstock, which leads to the destruction of useful minerals and an increase in their losses.
Effectively use the technological process of crushing using the discharge-pulse technology when crushing ore.
This is the only solution that provides not only a high grinding speed up to 0.8 -1mm, which is optimal for the further flotation process, but also a high material opening. If, after processing, you look at the ore under a microscope, you can see a lot of microcracks in the material. With such treatment, the coefficient of metal recovery from ore increases by 1.2 - 1.8 times.
Glass can be broken in the same way. This uses a different crusher device. Grinding is possible to sizes 3 - 10 microns.
All rights reserved by Trakonta 1996 – 2021