Trakonta ltd, 54031 Ukraine, Nikolaiv city, Electronnay street 81/4, E-mail: trakonta@gmail.com Tel: +380512714945; Mob, Viber: +380503180260

Electrohydropulse metal stamping
Parts of any shape and size can be stamped electrohydraulically. In the closed volume created by the discharge chamber and the workpiece, filled with water, high-pressure pulses are generated, generated by a high-voltage electric discharge, which deform the workpiece along the matrix adjacent to the discharge chamber. At present, based on the accumulated experience, electrohydraulic stamping is widely used. Several types of industrial electro-hydraulic installations for stamping parts have been created, the introduction of which has made it possible to significantly increase (5-10 times) labor productivity, simplify production, reduce metal consumption and equipment cost while improving the quality and reliability of products, and obtain a significant economic effect. Electro-hydraulic presses are capable of stamping blanks up to 2400 mm in size and up to 10 mm in thickness.
Trakonta ltd
Electrohydropulse metal stamping
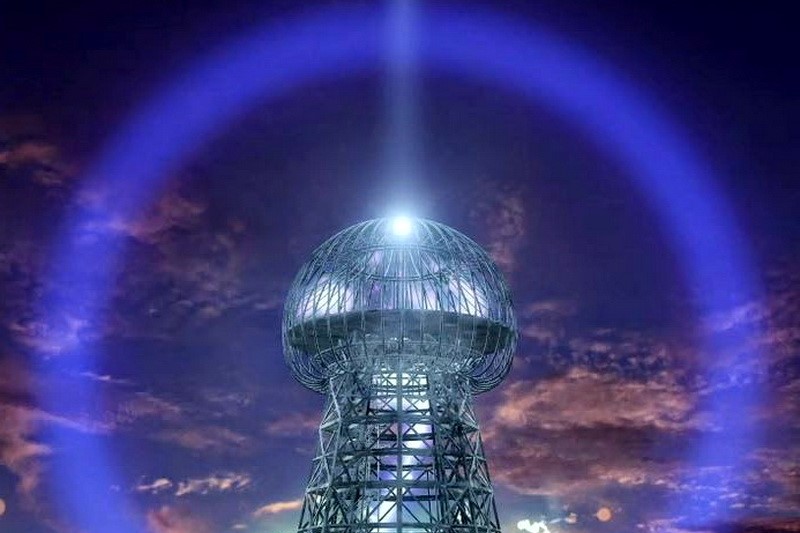
A significant technological effect is provided by the use of the method of stepwise energy supply to the discharge gap, which allows combining the advantages of operation at relatively low voltages with the advantages of operation at high voltages. This method also allows you to control the nature of the flow and the rate of deformation of the processed material. At the same time, a high voltage pulse is first applied to the working spark gap located in the electrohydraulic stamping chamber, but low energy, sufficient to breakdown this working gap and create an electrohydraulic shock, which makes it possible to transfer the processed material beyond the yield point, but insufficient to carry out the entire deformation work and complete manufacture of the product. Then, after a short period of time, adjustable in duration, a low voltage pulse is applied to the discharge channel that has arisen in the liquid, but high energy, sufficient to complete the entire work of stamping the already flowing material. This method allows the use of relatively low-voltage capacitors and power supply units, which are less bulky and not as expensive as high-voltage units corresponding to them in terms of power and energy.
Stamping of complex products of great length can also be carried out by sequential movement of the arrester over the product, the discharges of which form the product. In this case, the movable arrester can be delayed over the places of a complex profile or deep recess. For the same purpose, the second electrode of the working spark gap can be made in the form of a ring, and then the discharge will run around a circle.
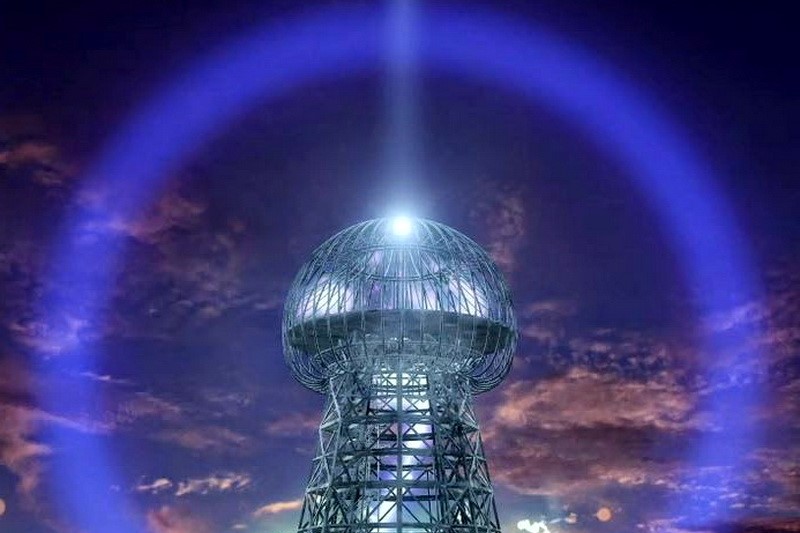
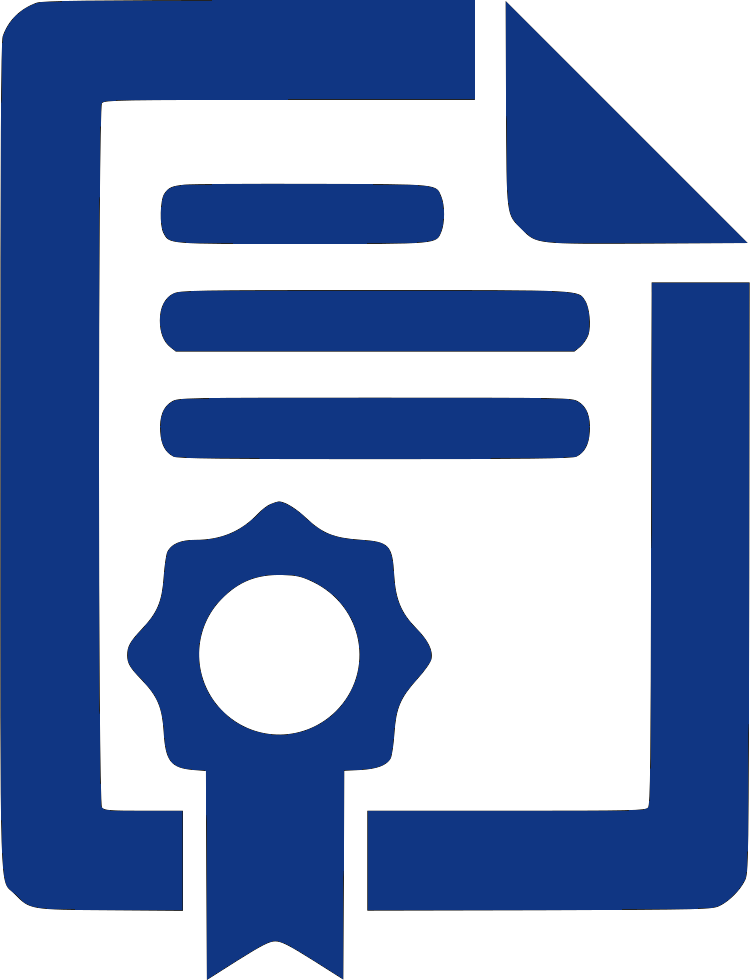
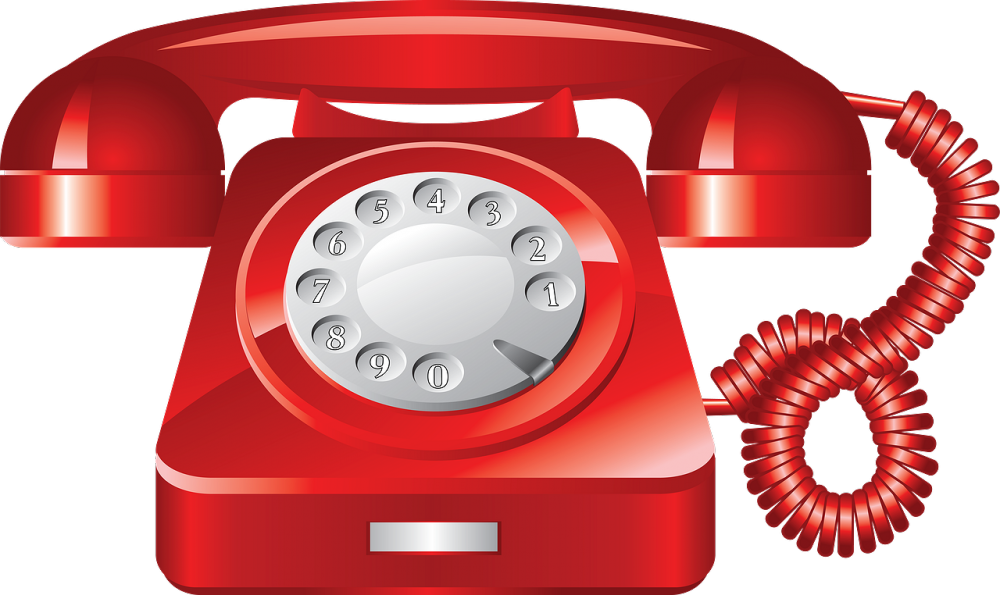

![]()
Currently, the most effective field of application of sheet electrohydraulic stamping is the shaping and calibration of conical and cylindrical shells with a diameter of up to 1200 mm at a height of up to 1100 mm from workpieces up to 5 mm thick. The range of thicknesses and overall dimensions of products made by electrohydraulic stamping continues to expand, depending both on the parameters of the current pulse generators and on the design perfection of the technological unit.
Known methods of stamping, drawing, bending and other deformation operations of plastic sheet materials involve the use of hydraulic or mechanical presses, in which the fluid pressure is created using pumping or compressor units. The electro-hydraulic stamping method provides for the implementation of these technological operations by electro-hydraulic pulses created in an open or closed chamber, the bottom, wall or cover of which is the material being processed. Electrohydraulic shocks are carried out during discharges between the electrodes and the material being processed or between two electrodes. The processed sheet material is pressed into the matrix under the action of an electrohydraulic pulse and thereby acquires its shape.
Electro-hydraulic stamping by spark discharge.
Electrohydraulic metal stamping can be performed using both low and high voltages. The convenience of storing high energies and switching high currents at high voltage is well known. But in modern conditions, the high cost and cumbersomeness of high-voltage capacitors often force us to abandon the further increase in the operating voltage of electrohydraulic stamping plants above a certain limit, which is mainly determined only by the mass and volume of capacitors produced by industry.
In electrohydraulic stamping, in order to avoid reverse deformation of products, a vacuum must be created in the die cavity under the stamped sheet, and the stamping chamber filled with liquid must be sealed. Vacuum under the product and overpressure in the punching chamber are recommended in all cases of stamping thin sheets with a sufficiently large product area.
For punching long channels, punching long holes or other similar work, the "traveling wave" method can be used. In this case, the alternation of spark discharges or thermal explosions, which are located along the length of the formed channel or hole, given in time, carries out successive deformation of a certain part of the product.
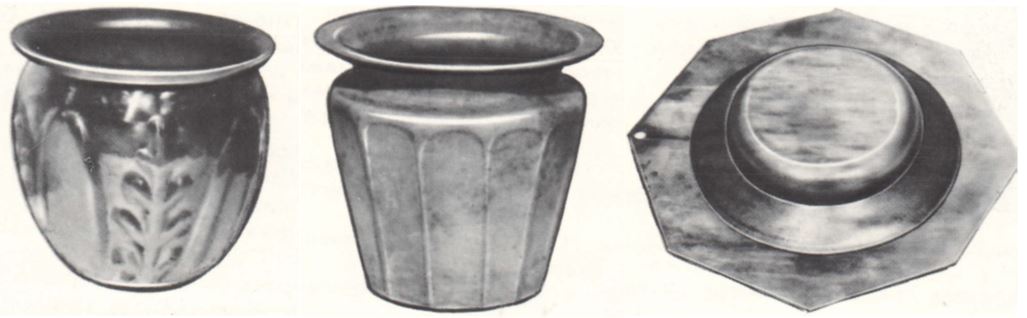
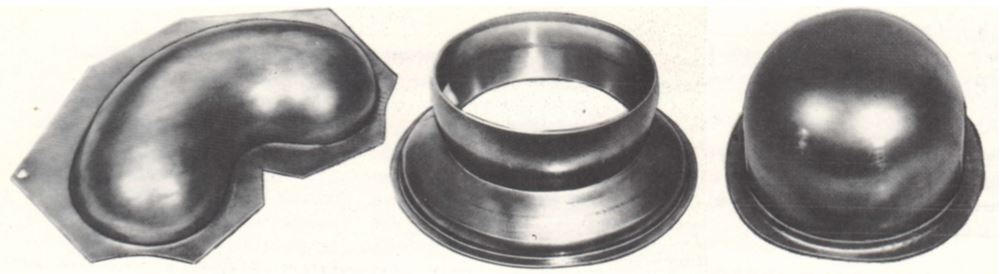
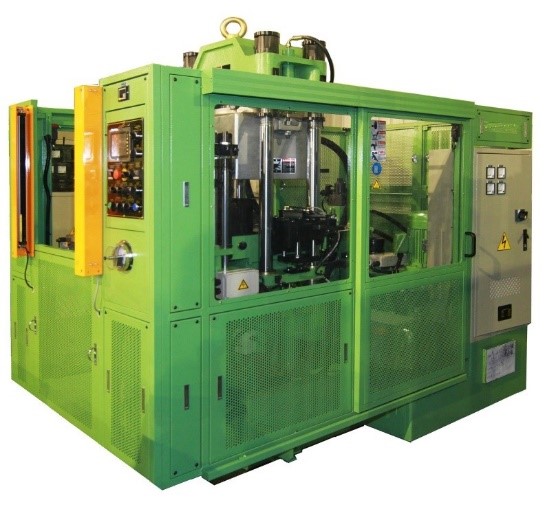
TECHNOLOGY PROVIDES:
- stamping of complex configuration parts from flat sheet and tubular blanks;
- punching holes of any shape in thin sheet parts on flat and curved surfaces, cutting out parts along the contour.
- combination of several stamping operations;
- restoration of the size of the worn-out surfaces of tubular parts by distribution (crimping) without subsequent machining;
- calibration of tubular parts, including welded shells of any diameter with internal ribbing;
- local deformation of large-sized parts.
TECHNOLOGY ADVANTAGES:
- the costs for the manufacture of die tooling are reduced, since water plays the role of a punch;
- technological transitions are reduced when drawing parts of conical, parabolic and spherical shapes;
- provides a more uniform thinning of the part in thickness;
- high quality of the surface of stamped parts and their dimensional accuracy is achieved;
- internal stresses of the part are stabilized after deformation, warpage of flat parts is reduced;
- reducing the cost of parts are stamped in small batches in experimental and pilot production, 5-10 times.
All rights reserved by Trakonta 1996 – 2021