ООО "Траконта" 54031 Украина, г. Николаев, ул. Электронная 81/4, E-mail: trakonta@gmail.com Tel: +380512714945; Mob, Viber: +380503180260
ООО "Траконта"
Электрогидроимпульсная штамповка металлов
Электрогидроимпульсная штамповка металлов
Электрогидравлическим способом можно штамповать детали любых форм и размеров. В замкнутом объеме, созданном разрядной камерой и заготовкой, заполненном водой, создаются импульсы высокого давления, генерируемые высоковольтным электрическим разрядом, которые деформируют заготовку по матрице, прилегаемой к разрядной камере. В настоящее время на основе накопленного опыта электрогидравлическая штамповка применяется весьма широко. Создано несколько типов промышленных электрогидравлических установок для штамповки деталей, внедрение которых позволило существенно повысить (в 5—10 раз) производительность труда, упростить производство, снизить металлоемкость и стоимость оборудования при повышении качества и надежности изделий и получить значительный экономический эффект. Электрогидравлические прессы способны штамповать заготовки размерами до 2400 мм при толщине до 10 мм.
В настоящее время наиболее эффективной областью применения листовой электрогидравлической штамповки является формообразование и калибровка конических и цилиндрических оболочек диаметром до 1200 мм при высоте до 1100 мм из заготовок толщиной до 5 мм. Продолжается расширение диапазона толщин и габаритных размеров изделий, выполняемых электрогидравлической штамповкой, зависящее как от параметров генераторов импульсов тока, так и от совершенства конструкции технологического узла.
Известные способы штамповки, вытяжки, гибки и выполнения других операций деформирования листовых пластических материалов предусматривают применение гидравлических или механических прессов, в которых давление жидкости создается при помощи насосных или компрессорных установок. Электрогидравлический способ штамповки предусматривает осуществление этих технологических операций электрогидравлическими ударами, создаваемыми в открытой или замкнутой камере, днищем, стенкой или крышкой которой служит обрабатываемый материал. Электрогидравлические удары осуществляются при разрядах между электродами и обрабатываемым материалом или между двумя электродами. Обрабатываемый листовой материал под действием электрогидравлического удара вдавливается в матрицу и тем самым приобретает ее форму.
Электрогидравлическая штамповка искровым разрядом. Электрогидравлическую штамповку металлов можно осуществлять как на низком, так и на высоком напряжениях. Удобства накопления больших энергий и коммутации больших токов на высоком напряжении общеизвестны. Но в современных условиях высокая стоимость и громоздкость высоковольтных конденсаторов зачастую заставляют отказываться от дальнейшего повышения рабочего напряжения установок электрогидравлической штамповки выше некоторого предела, определяемого в основном только массой и объемом выпускаемых промышленностью конденсаторов.
Принципиально при электрогидравлической штамповке нет необходимости в увеличении крутизны фронта и уменьшении длительности импульса, поскольку штамповка выполняется в основном за счет энергии запаздывающего потока, которая относительно больше на мягких, чем на жестких, режимах. Но более быстрый рост механического КПД разряда, возникающий вместе с ростом напряжения, приводит к тому, что при прочих равных условиях работа на высоких напряжениях, как правило, оказывается в общем энергетически и экономически более оправданной.
Значительный технологический эффект дает использование метода ступенчатой подачи энергии на разрядный промежуток, позволяющее совмещать достоинства работы на относительно низких напряжениях с достоинствами работы на высоких напряжениях. Этот метод также позволяет управлять характером течения и скоростью деформирования обрабатываемого материала. При этом на рабочий искровой промежуток, расположенный в камере электрогидравлической штамповки, сначала подается импульс высокого напряжения, но малой энергии, достаточный для пробоя данного рабочего промежутка и создания электрогидравлического удара, позволяющего перевести обрабатываемый материал за предел текучести, но недостаточный для осуществления всей работы деформации и полного изготовления изделия. Затем через короткий, регулируемый по длительности промежуток времени на возникший в жидкости канал разряда подается импульс низкого напряжения, но большой энергии, достаточный для завершения всей работы по штамповке уже текущего материала. Этот метод позволяет использовать относительно низковольтные конденсаторы и питающие установки, менее громоздкие и не столь дорогие, как соответствующие им по мощности и энергии высоковольтные установки.
Штамповка сложных изделий большой длины может также осуществляться и последовательным перемещением над изделием разрядника, разряды которого и формуют изделие. При этом над местами сложного профиля или глубокой выемки перемещаемый разрядник может задерживаться. С той же целью второй электрод рабочего искрового промежутка может быть выполнен в виде кольца, и тогда разряд будет обегать окружность, т. е. вращаться.
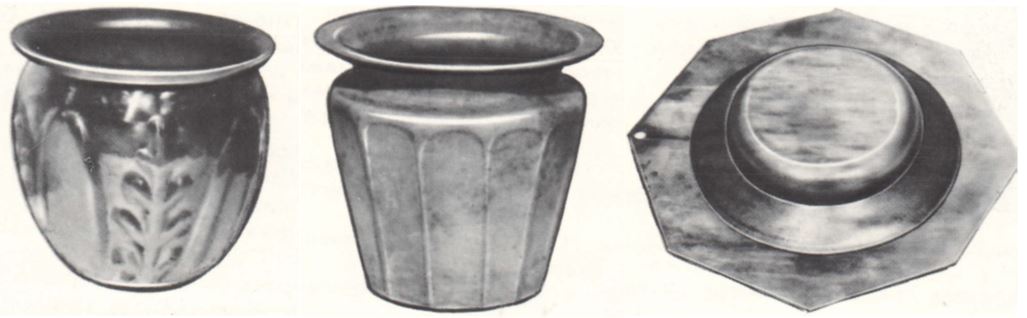
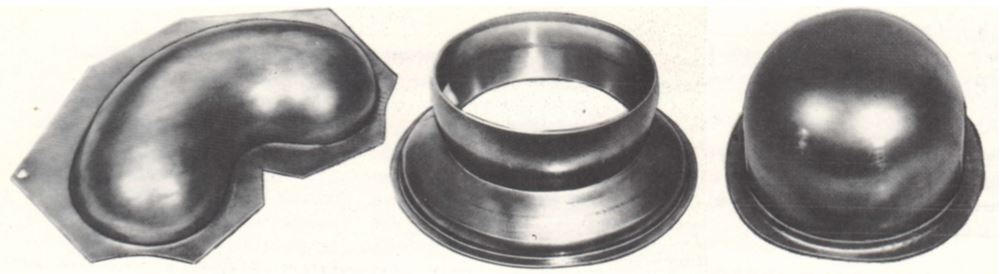
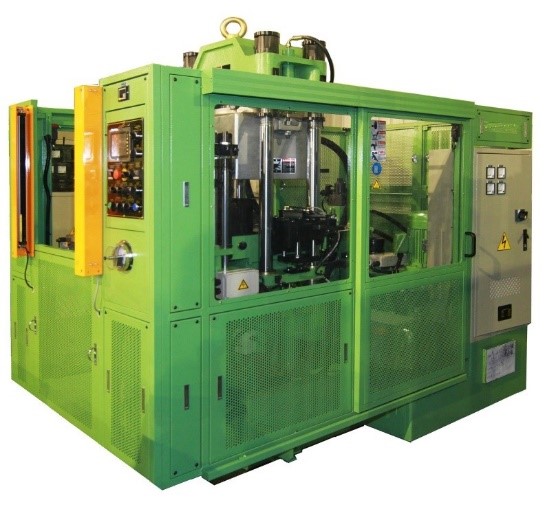
При электрогидравлической штамповке во избежание обратной деформации изделий в полости матрицы под штампуемым листом должен быть создан вакуум, а камера штампования, заполненная жидкостью, должна быть герметизирована. Вакуум под изделием и избыточное давление в камере штамповки рекомендуются во всех случаях штамповки тонких листов при достаточно большой площади изделия.
Для штамповки длинных каналов, вырубки протяженных отверстий или других подобных работ может быть использован метод «бегущей волны». При этом заданное по времени чередование искровых разрядов или тепловых взрывов, располагающихся по длине образуемого канала или отверстия, осуществляет последовательную деформацию определенного участка изделия.
ТЕХНОЛОГИЯ ОБЕСПЕЧИВАЕТ:
- штамповку сложных по конфигурации деталей из плоских листовых и трубчатых заготовок;
- пробивку отверстий любой формы в тонколистовых деталях на плоских и криволинейных поверхностях, вырубку деталей по контуру.
- сочетание нескольких штамповочных операций;
- восстановление размеров изношенных поверхностей трубчатых деталей путем раздачи (обжима) без последующей механической обработки;
- калибровку трубчатых деталей, в том числе сварных оболочек любого диаметра с внутренним оребрением;
- локальное деформирование крупногабаритных деталей.
ПРЕИМУЩЕСТВО ТЕХНОЛОГИИ:
- снижаются затраты на изготовление штамповой оснастки, так как роль пуансона выполняет вода;
- сокращаются технологические переходы при вытяжке деталей конической, параболической и сферической формы;
- обеспечивается более равномерное истончение детали по толщине;
- достигается высокое качество поверхности штампованных деталей и их размерная точность;
- стабилизируются внутренние напряжения детали после деформирования, уменьшается коробление плоских деталей;
- снижение себестоимости деталей штампуются малыми сериями в экспериментальном и опытном производстве, в 5-10 раз.
All rights reserved by Trakonta 1996 – 2021