Trakonta ltd, 54031 Ukraine, Nikolaiv city, Electronnay street 81/4, E-mail: trakonta@gmail.com Tel: +380512714945; Mob, Viber: +380503180260
Electrohydropulse processing of bast fiber materials
Electrohydropulse technologies are used in the textile industry, namely in the processing of bast fiber materials (flax, jute, ramie, hemp, kenaf, nettle and others).
As a result of the fast (microsecond) energy release of the capacitor, high (hundreds Co) temperature and pressure (tens of MPa) appear in the discharge channel. The effect of temperature on the medium is limited by the dimensions of the channel (no more than a few mm) and does not make any significant contribution to the processing, in contrast to the pulse pressure, the action zone of which is tens of cm, and the equivalent wavelengths of the impulse disturbance are in the millimeter range.
Trakonta ltd
Electrohydropulse processing of bast fiber materials
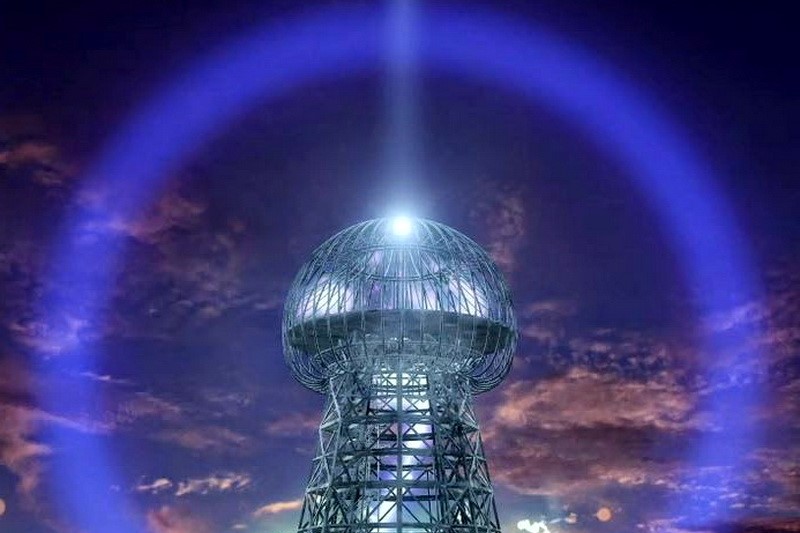
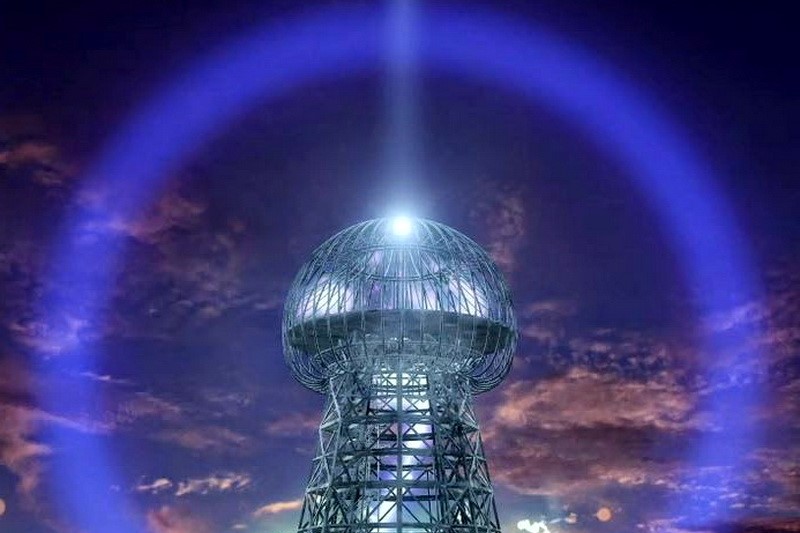
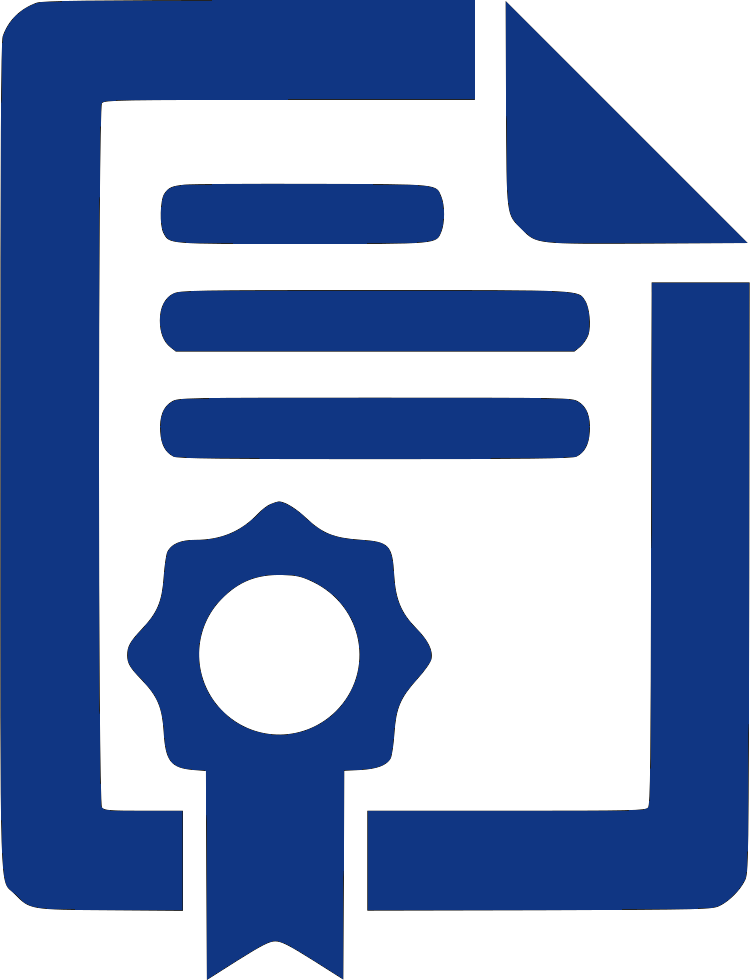
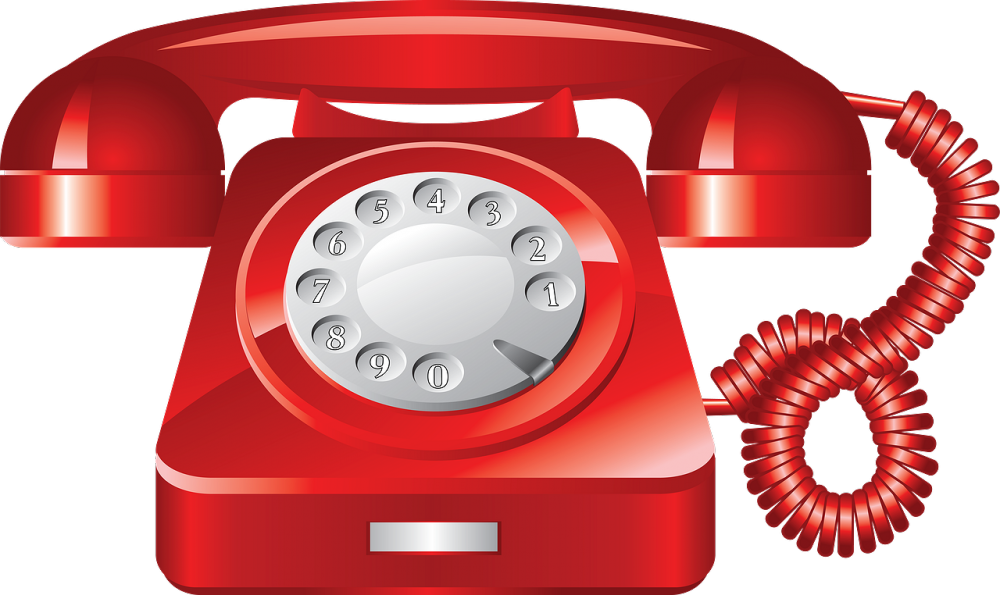

![]()
Physical phenomena during an electric discharge in water occur in the following sequence: first, a pre-discharge stage occurs, during which a discharge channel is formed, closing the interelectrode gap, then phenomena occurring when the capacitor energy is released in the discharge channel, and, finally, pulsations of the gas bubble after the discharge ... Thus, from the hydrodynamic point of view, a high-voltage electric discharge can be regarded as a process of expansion of a cavity in a liquid.
As a result of these phenomena, non-stationary processes of high-rate deformation, polymorphic changes, and motion of homogeneous and heterogeneous media are initiated, which occur at high values of energy concentration. These processes belong to the fast-flowing classes.
The essence of hydrodynamic treatment in a pulsed mode is that when a pulsed electric (spark) discharge is formed inside the volume of a liquid in a closed container, ultra-high hydraulic pressures arise around the zone of its formation, capable of performing useful mechanical work.
An electric pulse discharge in a liquid leads to a weakening of both pectin-containing and mechanical bonds between the elementary fibers in the bundle.
Since the essence of processing lies in the separation of the elementary fibers from each other while maintaining the integrity as much as possible, the central link for the production of cottonin is the weakening of the pectin-containing bonds, i.e. those bonds that glue both thin complexes of elementary fibers in a bundle, and bundles together.
Technological processes
Pre-loosened and purified fiber of bast-fiber crops (flax, jute, ramie, hemp, kenaf, nettle and others) enters the processing line, where it is soaked in a through bath 1 with water or a washing solution when it is completely immersed and moved along the bath with a fork device, water or washing solution are supplied simultaneously, but from opposite ends of the bath, or the fiber can be moved through the bath when soaked by means of a mesh conveyor while irrigating the raw materials and draining through the mesh holes. (Patent RU2280720C1).
The resulting partial mixing of raw materials during the advancement in the bath intensifies the fiber processing by removing air bubbles, dust and fertilizers, various compounds, including salts, which affect the process of cotonization.
It was experimentally established that during soaking and the temperature of the liquid for different types of raw materials are different. The temperature of the liquid ranges from +1 to + 90 ° C. When leaving the bath, the fiber is subjected to extraction by a squeezing device to remove the spent liquid. The pressing force is different for the formation of a controlled weight and volume of raw materials when fed into the device for cotonization.
Then the raw material enters the cotonization process, which is carried out by means of a device H, including a bath A for a liquid medium, a discharge chamber B installed in the bath and made in the form of a cap facing the open part to the bottom of the bath, in the upper part of which there are electrodes C connected to a current pulse generator PCG, camera B is mounted with discontinuous longitudinal movement and vertical movement in the loading zones E and unloading F by means of an element D connected in an electric drive G. В the cotonization device H on the fiber has an electro-hydraulic effect by creating an electric discharge between the electrodes C of the chamber B and the electrodes K located on the bottom of the bath.

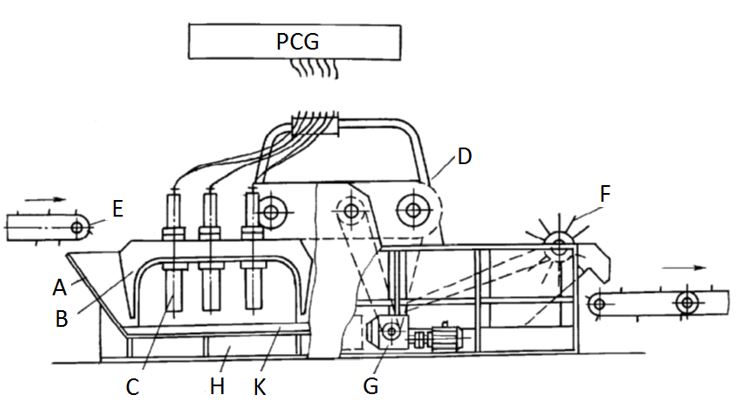
The dimensions and geometry of the discharge chamber, the electrical parameters of the pulse current generator, the pulse frequency, the length and geometry of the interelectrode space, the number of electrodes and the gap between them, the ratio of the mass of liquid to the mass of raw materials and other parameters are selected so as to create optimal efforts for the development of spark breakdown and shock configuration waves for efficient splitting and modification of various feedstocks and the best overall plant performance. Then the split (cotonized) fiber enters the second spin device.
The fiber pressed in the device is fed into the bath, where the fiber is bleached or washed, depending on the type of processed raw material.
After bleaching or washing, the wet fiber is loosened by the mechanical device, and then dried in the drying chamber.
Thus obtained fiber has a quality that allows you to use it in the production of a wide range of yarn, fabrics, non-woven materials, various products for technical, medical and domestic purposes.
This technology allows you to most fully extract valuable qualities from the spent liquid during processing by electro-hydraulic action.
When using this technology, the processing efficiency of various bast fiber material is increased and there is the possibility of multivariate use of line units to meet customer needs and achieve the most complete optimization of the bast fiber material processing technology.
All rights reserved by Trakonta 1996 – 2021